What is Lamborghini's "Forged Composite"?
Carbon fiber is known throughout the world in countless industries for its incredible strength-to-weight ratio. Typically, carbon fiber composites are interwoven strands of carbon sheets called "pre-preg" which is then impregnated with a special resin. Producing carbon fiber is expensive and time consuming but provides incredible strength per weight unit in the direction of the fibers. Automobili Lamborghini created their own internal division, "Advanced Composite Research Center" (ACRC), which handles all facets of Lamborghini's carbon production. ACRC's primary objectives are producing carbon components while simultaneously reducing costs and production time through innovative design and research of carbon fiber elements. After years of testing, research, and production optimization, Lamborghini unveiled their newly developed "Forged Composite" for the world to see.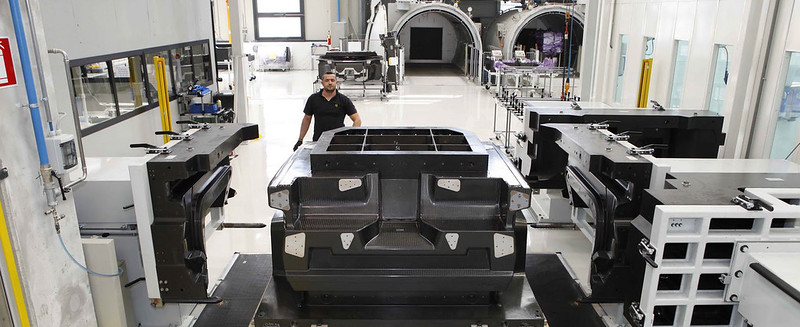


"Forged Composite" is in many ways different compared to the typical carbon fiber most know and love. For starters, "Forged Composite" is essentially a paste of carbon and resin that can be shaped or molded. To put it simply, it is compression molded in extreme heat. In detail, "Forged Composite" features shorter length carbon fibers and is unidirectionally stronger than typical carbon fiber. "Forged Composite" is created when the paste mixture of carbon and resin is pressed with 60 bar of pressure (870 psi) in a mold heated to 130 degrees Celsius. The benefits of this production method are: flexibility of producing complex parts from molds, extremely short curing time, cost reduction, and strength equal to or better than titanium at only 1/3rd the density. Curing time in a typical carbon fiber pre-preg production takes 6 hours, "Forged Composite" takes just under 9 minutes. Total production costs for "Forged Composite" are reduced by a staggering 30% compared to the production of the typical carbon fiber sheet. As you can see in the figures above, the benefits in regards to production are extremely enticing on all fronts.

Utilizing this new form of carbon, Automobili Lamborghini launched a new project to showcase their newly developed "Forged Composite". Thus, the "Sesto Elemento" concept was born from a standard Gallardo drivetrain. The Sesto Elemento was a technical exercise aimed to showcase the real world applications for this new form of carbon fiber. On the outside, "Forged Composite" loses the typical weave pattern and instead gains a marble-like appearance that is randomized and unique, similarly to how snowflakes are unique to each other. The Sesto Elemento's suspension arms, monocoque, crash structures, body shell, and even the high temp exhausts were all crafted from this new "Forged Composite". Featuring integrated racing bucket seats into the monocoque and titanium fasteners throughout, the Sesto Elemento weighed in at only 2,200lbs showing a 1,100lbs net reduction of weight from a standard Gallardo. This enables the Sesto Elemento to accelerate from 0-60mph in a mind-numbing 2.5 seconds with a power-to-weight ratio of 1:4. As if the performance figures weren't enough, the styling inside and out matched with sharp angles, hexagonal design details, and ferocity only a Lamborghini could dictate.


Lamborghini's ACRC department boasts a vast database and research facility that thoroughly examines, simulates, produces, and repairs carbon technologies. In regards to simulation, the ACRC department tests materials for behavior and characterization of carbon elements, components testing, corrosion tests, static and dynamic testing, along with production processes and methods. The Lamborghini Aventador features a complete carbon monocoque with front and rear subframes of aluminum. Should a Lamborghini Aventador ever require carbon repairs to its monocoque, a flying doctor who specializes in carbon repair is dispatched by air. The carbon repair specialist uses ACRC's inspection technologies that are non-destructive and utilize ultra sounds, thermography, and X-Ray examinations to learn about the condition of the carbon structures and elements. These non-invasive and non-destructive examinations allow the flying doctor to judge the damages to the carbon and evaluate the best strategy of repair for the composite structure. On top of ACRC's repair studies, ACRC also studies the corrosion characteristics, recyclability, and design of carbon composites.
Although production and utilization of "Forged Composite" is in its infantile stage, we can see "Forged Composite" in Lamborghini's all-new Huracán LP610-4. Specifically, the Huracán LP610-4's engine bay panels now have the optional "Forged Composite" finish, an all-new option for Lamborghini. Lamborghini also has set out to create exterior and interior components for the Lamborghini Aventador which were displayed at Geneva Motor Show of 2014 via Lamborghini's bespoke program, "Ad Personam". In 2014, Lamborghini also unveiled the Veneno Coupe and Veneno Roadster, a Aventador-based Carbon-masterpiece utilizing "Forged Composite" inside and out. All the exterior body panels are of "Forged Composite", as are the seatbacks, along with a mixture of Carbon Fiber and "Forged Composite" throughout the interior.


Currently, Lamborghini is the first and only manufacturer in the world to have received a Carbon Fiber repair certificate from TÜV. Lamborghini, with their own internal ACRC department, is also the only auto-manufacturer in the world to execute it all in-house, from simulation to production, and research. Currently, Lamborghini is testing and assessing the characteristics of "Forged Composite" in terms of age degradation, crash tests, & corrosion tests for future applications and uses. Just how far will Lamborghini take their "Forged Composite"? Only the future will tell.
No comments:
Post a Comment